Vacuum Insulated Glass in Historic Window Sash
Let's face it, anyone who's been involved selecting windows for historic properties has been presented with the antinomic choice between true reproduction windows and windows that meet contemporary building codes.
But what if a historic window sash could be fitted with glass that meets, or even far exceeds, building codes? Let's explore the concept and see how a new glazing technology makes this possible.
Why no good solution till now…The primary factor that makes it impossible to achieve strict historicity in window design while achieving the desired thermal performance is the limitations of the glass. Most building codes require a U-value of 0.35 (the lower the better) or below which is about 3.3 R value. The 1/8” monolithic glass, prevalent in historic windows has a U-value of about 1.2, which is an R value of less than 1.0 and, in most of the country, necessitates using a storm window* of some sort.
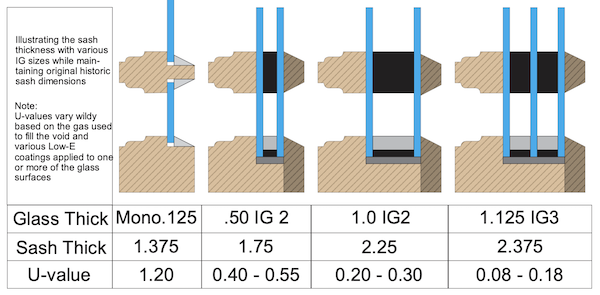
Conversely, the current maximum thermal performance in conventional glass configurations is as low as 0.08 (R-12.5) when utilizing expensive triple pane glass and exotic gasses and metallic film coatings (which create a very undesirable “shimmer” and reduced visible light transmittance). Insulated Glass thermal performance degrades from there, as the gas, films and lites are removed, down to well above the building code threshold of 0.35 for a two lite IG unit, with no gas or film – coming in at around 0.45 to 0.55 for a ½” overall unit.
So, it is possible to achieve reasonable thermal efficiency with conventional glazing configurations. However, regarding historic applications, the limiting factors are wall, jamb and sash thickness. Let’s review the dimensional constraints that a traditional historic window presents. See cross section below.
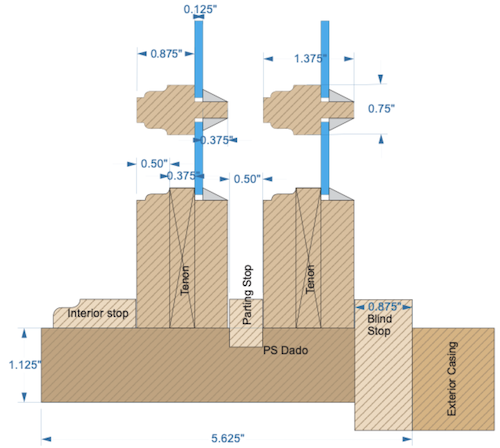
The wall thickness of most older frame homes is 5.5” (5 5/8” illustrated). That represents a true 2 x 4 stud, 7/8” sheeting on the exterior and about 5/8 of plaster and lath on the interior.
The jamb typically consists of (from exterior to interior) a 7/8” blind stop (with its exterior plane in the same plane as the sheeting), a 1 3/8” “track” for the upper sash, a ½” parting stop, a 1 3/8” “track” for the lower sash, then an interior stop which takes up the balance of the jamb thickness.
The sash is almost always 1 3/8” thick. It’s elements, from the interior to exterior, are the sash molding profile at 1/2”, a 3/8” flat that represents the tenon and a ½” “glazing rebate”. The glass is typically 1/8” and fits against the exterior face of the tenon flat, then the balance of the glazing rebate dimension is filled with 3/8” of glazing putty.
These dimensions form the character of a historic window system. There are numerous offsets from one element to another and these offsets serve to create the depth and shadow lines that make a traditionally constructed window so attractive and so different from a “flat faced” contemporary window, that lacks character and aesthetic appeal.
* Storm windows were first introduced in the 1930s. So, unfortunately, for homes built prior to 1930, even a conventional storm window is not a historically valid solution. In addition, storm windows are cumbersome, add additional cost, another layer of maintenance and significantly alter the appearance of the window unit in a deleterious manner. And, contrary to popular belief, storms only marginally increase the thermal performance since the air space between the glass lites is so great that it allows “thermal roll”, which has a negative impact on potential insulating value. Again, all the while, obscuring all the important details that define the historic window behind it. So here is the dilemma, in historic window applications; the maximum thickness of the glass can be no more than 1/8” to maintain all the other dimensions that are so important to the aesthetic character of the window unit. A glass dimension any greater than 1/8” will necessitate compromises elsewhere and the thicker the glass, the greater the compromise. Two particularly stubborn dimensions are the wall/jamb thickness and the distance between the blind stop and parting stop since the parting stop is in a dado cut into the jamb sides and head which determines the maximum thickness of the sash.
As you can see, there is no way to use anything but 1/8” glass without sacrificing important the traditional dimensions elsewhere, yet insulated glass is mandatory to achieve acceptable thermal performance. It’s obvious that trying to integrate standard IG into traditional sash, while maintaining historicity, is a futile effort. However, a new glass technology has recently become available in the US that promises to upturn the insulated glass industry. The genre is called VIG for Vacuum Insulated Glass.
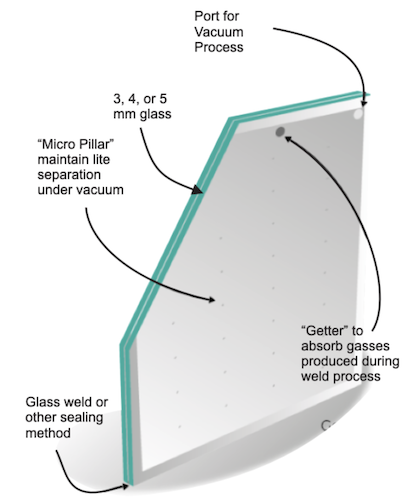
The concept is simple, but the execution is extremely difficult and manufacturing intensive. Two lites of 3-, 4-, or 5-mm glass (it’s all metric and end up being approx. ¼”, 5/16” or 3/8 thick units) are separated by only approximately .2 mm. Then somewhere in the process, a glass weld is applied around the edges of the unit and the air is vacuumed from the miniscule air space (or vice versa). Since there is nothing between the lites to transfer heat, amazingly low U-values can be achieved. Some 6 mm (1/4”) units have .021 U-factor, (half again better than most ¾” IG) or better, and some 8 mm units have a 0.06 U-factor and boast an R-18 performance!
Window and glazing companies are beginning to implement VIG in commercial curtain walls and some top of the line contemporary residential windows but, practically ignoring the historic market. Fortunately, there one or two manufacturers focused on the historical market that are embracing this technology. And, for good reason – this means that this building code busting performance can be applied to historic windows by only slightly modifying sash and/or jamb dimensions. These modifications can be so slight to not be visually perceptible. Let’s look!
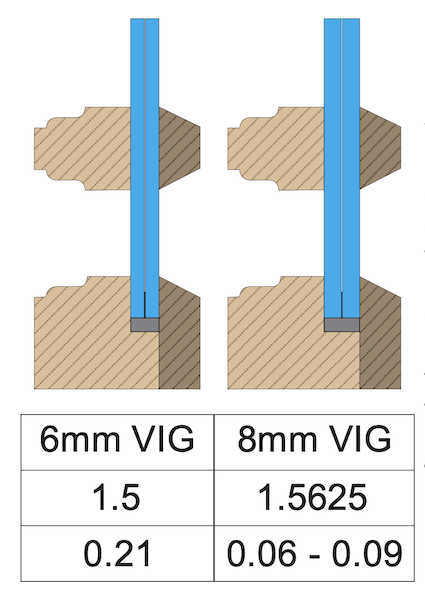
Here are a 6mm and an 8mm VIG unit fitted to typical 1 3/8” residential traditional sash. As you can see, the sash thickness only increases by about 1/8” for the 6mm and about 3/16 for the 8mm. Because the jamb can be designed around the sash of a new-construction unit, nothing will change except the width of the interior stop. Thus, perfect fidelity to the traditional dimensions is maintained while code satisfying and comfort enhancing performance is added!
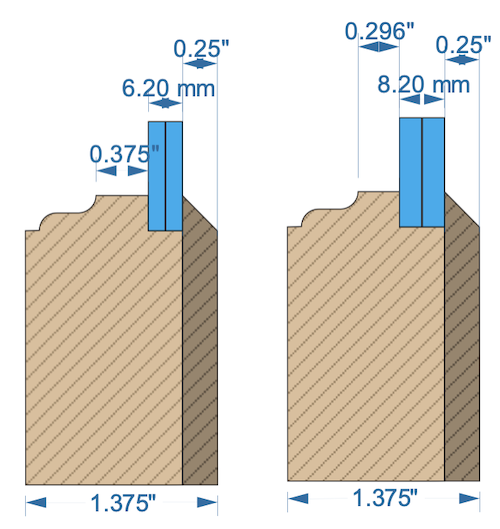
When the subject is a “replacement sash system”, which allows simple (DIY) removal of original sash and replacement with new sash with the same thickness, height and width, a few other modifications are necessary but, inconspicuous, nonetheless. This application involves merely reducing the exterior return from .375 to .25 and the tenon shoulder remains 0.375” for 6mm glass and decreases slightly to 0.296” (about a 1/16” reduction) for the 8mm glass.
VIG is not without some minor drawbacks.
“Micro pillars”, which are required to keep the lites separated under vacuum, are extremely small and practically imperceptible but indeed visible on close inspection. One window company with thousands of residential units in the field reports, “once they are made aware of the pillars, people are initially concerned but, once the windows are installed, they universally report they no longer even notice them”.
Many manufacturers use a port about 1” from one corner of the unit and cover this with a ½” diameter “vent cap”. The vent cap is indeed visible and a source of concern for some. But, like the pillars, consumers become inured to their presence. This is particularly true when the cap is placed in the upper left and lower right corners of a double-hung window. Since the lower is usually well below the normal field of vision and the upper, also outside the field of vision, is often covered by window treatments, the ports become a non-issue. There is at least one manufacturer that evacuates the air through the edge of the glass and, since the edge seal is buried in the glazing rebate, has no visible port.
Regardless of the manufacturer, VIG is more expensive than standard IG. Of course, the price of VIG is all over the board, with the least expensive being over half again the price of standard IG, all the way to four times its cost. This difference will be reflected in the overall price of the window. But, since the glass is only one component of the window unit, the VIG upgrade only adds 20% to 35% to the cost of the entire window.
The fact that some sort of vent port is required makes VIG an unlikely candidate for use in True Divided Lite windows, because among other things, rather than a single port per sash there would then be a port in every lite and indeed become an aesthetic issue. On the other hand, VIG in a Simulated Divided Lite application is far superior to standard IG because the lites of a VIG are so close together they look like a single piece of glass. HPC review architects and other historic window professionals have stated they can not tell that an SDL VIG sash is not TDL!